Teilen Sie Ihre Erfahrunge und Wünsche mit uns und anderen Usern!
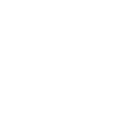
custom data type
Hello,
I am working on importing signals with a custom data type like a structure using PLCSIM interface. I have an error saying that it is not supported. Do you have any method so that I can use these structure in Unity?

Hi Kévin,
currently we have no solution to support hat. It would require a support of this flexible data definition of the PLCInput and -Output side in Game4Automation and it would need to be implemented into the Game4Automation PLCSim Advanced Interface. There are currently no plans for that development.
Best regards
Thomas
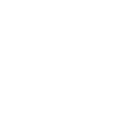
S7 connection
Hello,
I have started to use S7 TCP-IP to connect to TIA Portal with PLCSIM advanced. When I think they are connected and I tried to force a signal at true, in the TIA program I see the corresponding signal blinking irregulary.
Do someone have this problem or how to resolve it?

It depends what you want to do. Because of Limitations in Unity PLCSim Advanced is a little bit more complicated (external coupling exe needs to be started). S7 Interface is easier and works on all Platforms. But with S7 interface you can't write to inputs where also a hardware is configured to.

I can't read the plc input signals
Dear Thomas.I connect S7-1200 PLC to unity,but when I import Outputs it is OK,when I import Inputs it doesn't work,I want to make a digital twin project.Can I just read the inputs and I can change the models depend the inputs status,I don't write it or change it.If my unity models want to know the inputs status,what should I do?

Hard to say where your problem is. But Input and Outputs are working if the inputs don't collide with a real hardware input. If you problem still exists please create a very simple example (S7 project and Unity project) and send it to us.

I can't find the component(Xde Rigid Body)
Hello!Dear Thomas!
When I Enable Interact,it shows:
But I have buy it and I can't add component like the video(
Accurate Physics with Game4Automation
)My unity is 2020.3.4 and game4automation professional is running well.

How to install
Hello ,
I just buy Game4automation pro and conveyor but i can´t install .
My instalation fail . I try to follow the manual but without sucess.
According the manual new menu should appears but on my case it dont appears :
https://game4automation.com/documentation/current/installation.html#Check-if-a-new-menu-is-available
I can import the package from the store but not like the same procedure that is on the manual .
I just press on the bottom import on the store.

You should have any kind of error in the console log which should point you in the right direction.
Please always check and send us the log in case of problems.
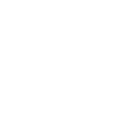
Share-Space for custom Behavior Scripts
Hi,
is it possible to implement some kind of share space into the forum or website, where users can upload their custom made scripts to extend the functionality of the implemented behavior scripts?

S7 interface DB write bug
I write in S7 interface in DB1.DBX1.0 but on PLC it is writing in DB1.DBX1.1
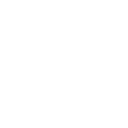
s7
Hello
I played a little bit with the conveyor and the sensor form the starter tutorial. I noticed that if a MU is occupying the sensor and then I delete the MU either manually or with a think, the sensor continues to be occupied. In order for the sensor to be free, I first need to move the MU out of the sensor collision box and then I can delete it. In my opinion the senor shouldn't remain occupied if the MU that occupies the sensor is deleted.

Hi,
nice work. How did you connected to KUKA.
There seems to be still a cycle time problem. If you would like I could support you, if you support me for getting it into the Professional version ;-)
Best regards
Thomas
Customer support service by UserEcho