Teilen Sie Ihre Erfahrunge und Wünsche mit uns und anderen Usern!

Unity Build Player Window error
Hello , I have errors when i trying to build player window , its works when i delete game4automation , and if i add game4automation and trying to compile i get some errors , I want to mention that I did not add the s7 interface, I did not add anything

Problem was solved by deleting Parts4Cad and Zip in Tools. Included ZIP is not compatible with UWP. We will change that in future.

S7 plc i want to show on scene value from the controller
Hello , i want to show value from the controler as a text on scene , how i can do that?

Hello,
you need to do it with a little script that takes Signal.Value and which is putting this into a Unity UI text box.
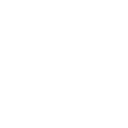
S7 interface plc input write error CPU : Function not available
Helo. Im trying to connect s7-1200 with game4automation. I saw the tutorial video and the https://game4automation.com/documentation/current/s7tcpip.html.
I followed all the process but still not working with this signs keep cycling.
I successfully checked the connection and added sdf file as well.
S7 interface plc input write error CPU : Function not available
I don't know how to solve this problem. Thank you.

Hi, sorry for my late response. We needed first to support the open issues of our professional customers.
I checked your project but it seems that I don't have all data to be able to reproduce your problem. I would need your full S7 project. And you need to tell me which scene to open and what else to do to get the same problems as you do. Thanks.
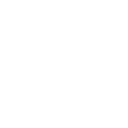
Error opening game4automation project in a different PC
I've started a project with the game4automation asset. I have a robot connected with the roboDK interface. When I try to open the project with another PC, It appears this error:
ArgumentNullException: Value cannot be null.
Parameter name: String
System.Number.StringToNumber (System.String str, System.Globalization.NumberStyles options, System.Number+NumberBuffer& number, System.Globalization.NumberFormatInfo info, System.Boolean parseDecimal) (at <9577ac7a62ef43179789031239ba8798>:0)
System.Number.ParseInt32 (System.String s, System.Globalization.NumberStyles style, System.Globalization.NumberFormatInfo info) (at <9577ac7a62ef43179789031239ba8798>:0)
System.Int32.Parse (System.String s) (at <9577ac7a62ef43179789031239ba8798>:0)
game4automation.PLCOutputInt.SetValue (System.String value) (at [old PC Path]/PLCOutputInt.cs:58)
game4automation.RoboDKInterface.UpdateSignals () (at [old PC Path]/RoboDK/RoboDKInterface.cs:320)
game4automation.RoboDKInterface.CommunicationThreadUpdate () (at [old PC Path]/RoboDK/RoboDKInterface.cs:537)
game4automation.InterfaceThreadedBaseClass.CommunicationThread () (at [old PC Path]/InterfaceThreadedBaseClass.cs:50)
System.Threading.ThreadHelper.ThreadStart_Context (System.Object state) (at <9577ac7a62ef43179789031239ba8798>:0)
System.Threading.ExecutionContext.RunInternal (System.Threading.ExecutionContext executionContext, System.Threading.ContextCallback callback, System.Object state, System.Boolean preserveSyncCtx) (at <9577ac7a62ef43179789031239ba8798>:0)
System.Threading.ExecutionContext.Run (System.Threading.ExecutionContext executionContext, System.Threading.ContextCallback callback, System.Object state, System.Boolean preserveSyncCtx) (at <9577ac7a62ef43179789031239ba8798>:0)
System.Threading.ExecutionContext.Run (System.Threading.ExecutionContext executionContext, System.Threading.ContextCallback callback, System.Object state) (at <9577ac7a62ef43179789031239ba8798>:0)
System.Threading.ThreadHelper.ThreadStart () (at <9577ac7a62ef43179789031239ba8798>:0)
UnityEngine.<>c:b__0_0(Object, UnhandledExceptionEventArgs)
It seems like some paths from the old PC are still remembered by the asset. I have changed the RoboDK Application path and the RoboDK file path, but the error stays. Reinstalling the asset just works, but it is uncomfortable to do it every time I switch to another PC.

If you changed the RoboDK pathes I don't know why it not opens. The code is always just using this path. Is your path somehow uncommon with special characters or empty spaces?
You might need to set some breakpoints in RoboDKInterface.cs and check what is going wrong. If you don't find the issue we should do a Zoom Session and I will check on your computer.

Grip scripts teleports mu to a different location
Hi I'm having an issue with the grip script which I placed on a rotary arm on the automatic machine I'm designing, when the PLCOutputBool I use to pick the designated mu goes to true the MU that should be picked up and placed immediately teleports to a different location. My grip works just fine, but the mu will be moved on the location where it was teleported instead of attached to the gripper. I will include some pictures to better explain the issue.
In the first picture the green arrow points to the gripper and the red one to the mu.
In the second one, you can see how the mu (red arrow) is teleported to a different location immediately just as the signal linked to "Signal Pick" is true.
The pivots of the sensor linked to "part to grip", of the gripper and the pivot of the rotary arm correctly set. The Pivot of the game object representing all the automatic machine (highest in the hierarchy) is located also on the red arrow in the secon picture.
How do I fix this issue?
Thanks
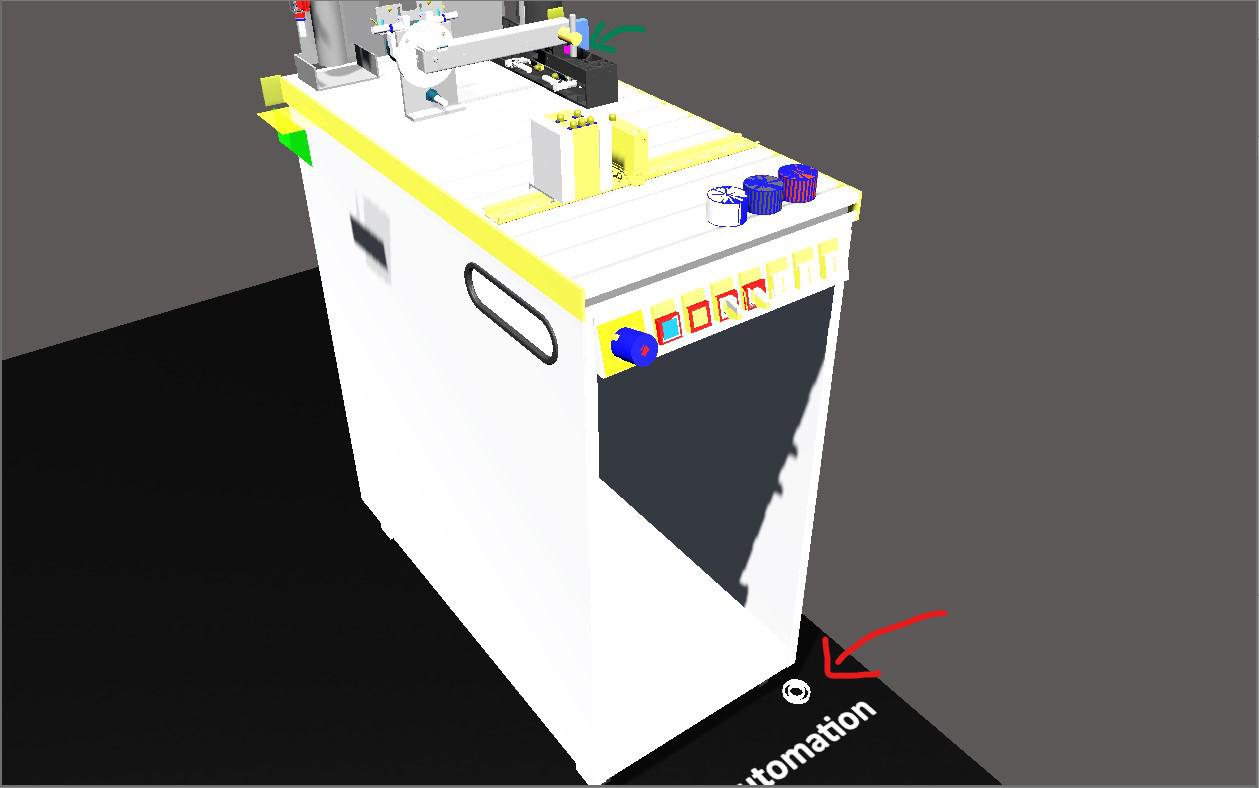

Sorry for my late response.
Grip should work. Please check how we did it in our dem model.
You can upload your model via https://game4automation.com/send and I will check what is missing in your project.
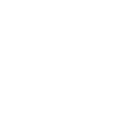
Interface to SIMIT via SHM unstable
Hello,
with my coupling between SIMIT and G4A the connection always breaks down.
I suppose it is due to a timeout at G4A. Because there is a high simulation load at SIMIT at the time of interruption. I can use the "Import Signals" button to reestablish the connection, but the connection does not persist.
Can I activate a cyclic reconnect if the connection is not established?
Thanks in advance
David

There will be a value in the next release which will allow to configure the "no responding" time which will set the interface to disconnected.

reading from plc not possible
I have added the a sensor from my PLC but as soon as i start running my program it writes a value. I would like to read the current value and not write anything. This is what my sensor looks like when it is added: Many thanks!

OK but usually PLC Inputs should only be written by Unity and not read.
You could manually create your table using excel (in the form TIA Portal is creating the tables) or you could manually create the IOs in Unity. Please delete the spaces in the names so it should for example be "I5.0" and not "I 5.0"). Maybe this is also an issue.
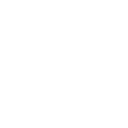
Compile Problems with demogame4automation
Hello I recently purchased the game4automation asset to test the features that it offers but I´m having problem with the demo compilation..
I followed the guide but unfortunately due to the new versions of unity, some steps are different.
Those are some of the errors that i get when I try to run the demo:
And for example when I configure the "build project settings" I cannot find the called "scripting runtime version" and maybe that's the reason.. I just can configure following:
Do you have some Idea what is going on?

It should work with some minor changes which you would need to do on your own. Officially, we only support latest LTS releases.
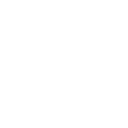
S7 TCP Interface DB access
Is it possible to direct access variables which are stored in DBs with the Siemens TCP Interface? The problem there is, that in the TIA variable table only M,Q and I are allowed, but the actual style of programming a Siemens CPU is to store global data in DBs. Merker are not used anymore. I dont want to reorganize the variables of the project for the simulation.
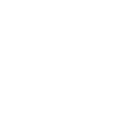
S7 interface problem
Hello,
I was following the youtube tutorial on how to connect Unity with S7 controller (in my case 1500).
After I successfully checked the connection and added PLCTags sdf file, made a fast test scene but when I Play it I have the following messages cycling:
Any suggestions ?

You are welcome, please give us a good rating in the Unity asset store if you are happy with our solution - thanks!
Customer support service by UserEcho