Teilen Sie Ihre Erfahrunge und Wünsche mit uns und anderen Usern!

Is it possible to make an executable game-file linked to PLC?
Hey!
I have managed to get the OPC UA -connection working with while inside Unity Editor's Play-mode, but when I try to Build into an .exe, the OPC UA -connection no more works. Is there a solution to this?

The Upgrade Message is always there - if you can use and add OPCUA and other Professional features you are having the professional version. Will let you know when the Beta is available. B
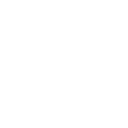
s7
Hello
I played a little bit with the conveyor and the sensor form the starter tutorial. I noticed that if a MU is occupying the sensor and then I delete the MU either manually or with a think, the sensor continues to be occupied. In order for the sensor to be free, I first need to move the MU out of the sensor collision box and then I can delete it. In my opinion the senor shouldn't remain occupied if the MU that occupies the sensor is deleted.
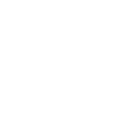
Is it possible to write to a Bool in DB with S7. e.g. PLCInputBool to DB43.DB145.0
Hello. I'm thinking it isn't possible to write to a Bool in DB, but maybe I haven't tried the right format. Any tips? Thanks.

Hello,
writing to DBs is described here and it should be possible what you like to do:
https://game4automation.com/documentation/current/s7tcpip.html#Reading-and-Writing-DBs
I think it should be DB43.DBX145.0
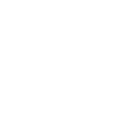
g4a duplicates Script
I am building some UI Elements to write PLCOutputFloats (bool, etc) from Input fields, toggles and buttons.
Spontaneously I am getting errors because of ambigious names for these PLCOutput classes.
Somehow g4a duplicates the classes so I get a PLCOutputBool1.cs
Can you explain what´s wrong?
Best regards
Benedikt

G4A itself for sure not duplicates classes. Currently I don't know why this happens. Please delete the duplicated classes.
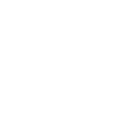
Import problem with Pixyz
The Import and update with the Pixyz Plugin does not work since updating to Unity 2019. The workaround you, Thomas, explained to me does not work. I can´t compare the Current and Update. The Problem is that the JT_Prop_Name does not appear in the Metada of the CAD-File. I get an error ".....is not unambigious". The Updater does not detect that the CAD-File changed during update.
Pixyz said the plugins API will work with the next update which is going to be released around the end of February.
Can you put that on your issue list so that it will work as soon as possible? The Updater is very important for us.
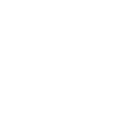
Sensor "Limit Sensor To Tag" null Error
I have encountered a few error from sensor script:
The sensor script throws a null error when using the "Limit Sensor To Tag" function unless the parent object have a MU.
Even though I am using the "Limit Sensor To Tag" function the sensor still gets trigger by the parents objects of the object that have the tag. (Parents objects do have mesh collider attached)

Hi Dat, I just checked. Objects wich are colliding with the Sensor must alway have the MU script on the same or in a level above the collider. This is the planned behaviour. I don't know in what combinatione exactly your problem comes up. Can you send me a simple example?

VR in Game4Automation
Hello forum
I bought an Oculus Quest 2 headset last week and I would like to know if its possible to connect it to the demo of Game4Automation.
Is there any resource about how to use VR in Game4Automation?
Thanks in advance and please, try to translate the menu of the forum cause we all arent german :)

Hello Pablo,
G4A is fully compatible with more or less all VR/AR solutions you can find for Unity.
you should follow the Occulus Documentation:
https://developer.oculus.com/documentation/unity/book-unity-dg/
Or you could use Steam - the advantage with Steam is that it works with most VR headsets on the market:
https://valvesoftware.github.io/steamvr_unity_plugin/articles/Quickstart.html
At the end, you need to integrate with all that VR Applications some standard Assets in your project and in your scene some standard components like VR Camera, Teleport and so on. You will need to deactivate or delete the G4A Camera because camera movement will be replaced by the VR application.
Maybe I will do soon an official tutorial about that. But if you follow the VR documentations and tutorials on the web you should be able to do that.
And sorry, did not notice, the forum is now also in English...
Best regards
Thomas

Unity Build Player Window error
Hello , I have errors when i trying to build player window , its works when i delete game4automation , and if i add game4automation and trying to compile i get some errors , I want to mention that I did not add the s7 interface, I did not add anything

Problem was solved by deleting Parts4Cad and Zip in Tools. Included ZIP is not compatible with UWP. We will change that in future.

Hi,
nice work. How did you connected to KUKA.
There seems to be still a cycle time problem. If you would like I could support you, if you support me for getting it into the Professional version ;-)
Best regards
Thomas

S7 plc i want to show on scene value from the controller
Hello , i want to show value from the controler as a text on scene , how i can do that?

Hello,
you need to do it with a little script that takes Signal.Value and which is putting this into a Unity UI text box.
Customer support service by UserEcho